ENVIRONMENTAL
AUTHORIZATION
ENVIRONMENTAL
AUTHORIZATION
Mining lease with the Québec Minister of Natural Resources and Forests for the Rose Lithium-Tantalum project: One of the most advanced hard rock lithium projects and only North American lithium projects with environmental authorization.
AGREEMENT WITH
FIRST NATIONS
AGREEMENT WITH
FIRST NATIONS
The Pikhuutaau Agreement provides for the collaboration and participation of the Crees with Critical Elements Lithium Corporation to ensure environmental monitoring and reflects the efforts to manage the relationship during the next project stages.
EXPANSION
POTENTIAL
EXPANSION
POTENTIAL
Critical Elements Lithium continues to expand major discovery at Rose West with additional multiple wide lithium-rich intercepts. We recognize the opportunity to add significantly to the Rose Project’s resource inventory and, potentially, augment its mine life and economics.
100% owned and located in northern Quebec on the territory of Eeyou Istchee James Bay
- The Nemiscau airport services the regions air travel needs.
- The Rose property site is located 50 km by road from the Nemiscau airport.
- 80 km south of Goldcorp’s Éléonore gold mine
- 45 km north-west of Nemaska’s Whabouchi lithium project
- 20 km south of Hydro Québec’s Eastmain 1 hydroelectricity generating plant.
ROSE LITHIUM-TANTALUM HIGH PURITY DEPOSIT WITH FEASIBILITY STUDY
The Rose Lithium-Tantalum Project is 100%-owned by Critical Elements. The Corporation’s market strategy is to enter the lithium market with a low-risk approach. The completion of the Feasibility Study on the spodumene plant is the first step to entering the market and establish the Corporation as a reliable high-quality lithium supplier. The low-risk approach is characterized by simple open-pit mining and conventional lithium processing technologies.
Critical Elements has consistently sought to advance the wholly-owned Rose Lithium-Tantalum Project in a low-risk manner. To this end, the Corporation has completed a new Feasibility Study with a conservative spodumene concentrate price deck, as well as capital and operating cost estimates reflective of current market conditions. The new Feasibility Study incorporates a standard truck and shovel open-pit mining operation and conventional lithium processing technologies. The Project will produce technical grade spodumene concentrate for the glass and ceramics industry and chemical grade spodumene concentrate for conversion for use in batteries for e-mobility, as well as a tantalite concentrate.
The mine will excavate a total of 26.3M tonnes ore grading an average of 0.87% Li2O and 138 ppm Ta2O5Â after dilution. The mill will process 1.61M tonnes of ore per year to produce an annual average of 203,765 tonnes of technical and chemical grade spodumene concentrates and 580 tonnes of tantalite concentrates. The ore is contained in several parallel and continuous shallow dipping pegmatite dykes outcropping on surface. The ore zones are open at depth and a future underground operation is possible.
Over the life of mine, the open pit will excavate a total of 182.4M tonnes of waste rock and 10.9 M tonnes of overburden. The average strip ratio is 7.3 tonnes of waste per tonne of ore.
After-tax NPV8% of US$2,195 million, after-tax IRR of 65.7%
Average annual production
- Average production Year 2-17:Â 157,706 tonnes of chemical grade 5.56% spodumene concentrate.
- Average production Year 2-17:Â 46,059 tonnes of technical grade 6.16% spodumene concentrate.
- Average production Year 2-17:Â 580 tonnes of tantalum concentrate.
- Average operating costs: US$81,30 per tonne milled, US$587 per tonne of concentrate (all concentrate production combined)
- Estimated initial capital cost: US$471 million (before working capital)
- Average gross margin: 78.8%
After-tax NPV8% of US$2,195 million, after-tax IRR of 65.7% and Average price assumptions of US$4,699 per tonne technical grade lithium concentrate, US$2,162 per tonne chemical grade lithium concentrate and US$150 per kg tantalum pentoxide (Ta2O5).
Anticipated construction time: 21 months to start of production
OPEN-PIT MINING AND CONVENTIONAL LITHIUM PROCESSING TECHNOLOGIES
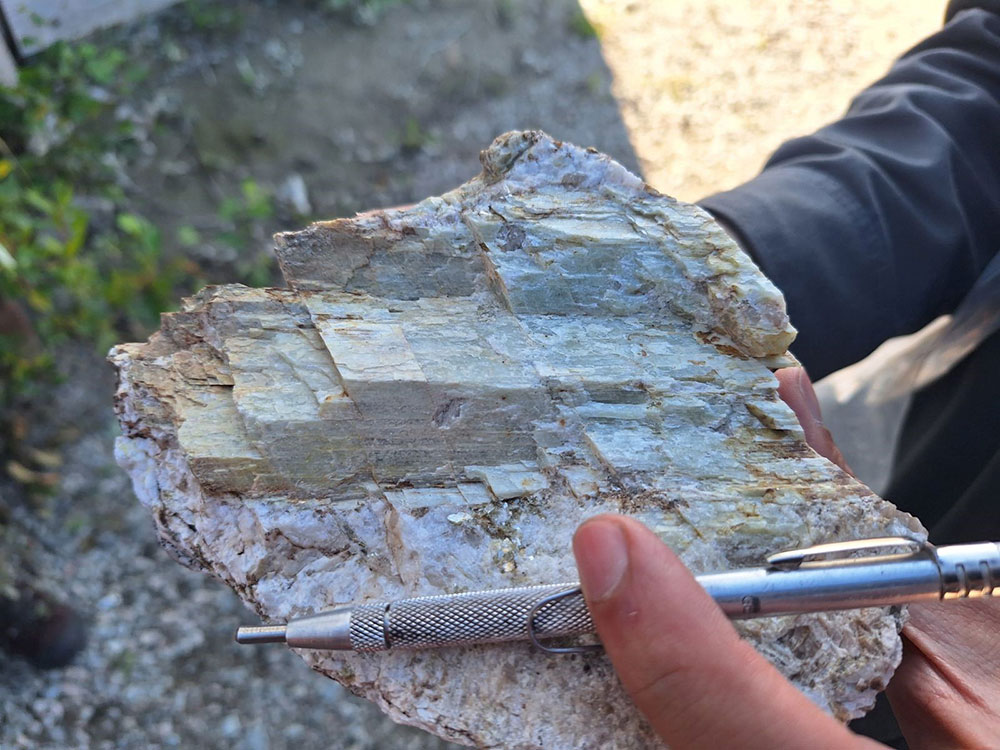
Operating costs are estimated at US$81.30 per tonne of ore processed
ECONOMICS 1,2,3 | Units | Value |
---|---|---|
Initial Capital Cost Estimate before working capital | US$M | 471 |
After-Tax Cash Flow | US$M | 3,352 |
After-Tax NPV 8% | US$M | 2,195 |
After-Tax IRR | % | 65.7 |
After-Tax Payback Period | Years | 1.8 |
Average operating costs: US$81,30 per tonne milled, US$587 per tonne of concentrate (all concentrate production combined)
|
AFTER-TAX NPV8% OF US$2,195 MILLION, AFTER-TAX IRR OF 65.7%
The mine will process 1,610,000 tonnes ore per year grading an average of 0.87% Li2O and 138 ppm Ta2O5Â over a period of 17 years.
Operating Costs
The operating costs are estimated at US$81.30 per tonne of ore processed which include:
- Mining: US$27.05 per tonne processed
- Processing: US$20.79 per tonne processed
- G&A : US$15.94 per tonne processed
- Concentrate transportation: US$17.52 per tonne processed
The total operating costs are estimated at US$587/tonne of concentrate after Tantalite Credit.
Energy unit costs are estimated to CA$0.055 per kWh for electricity and CA$1.35 per litre for diesel.
Capital Costs
The capital and operating costs were estimated in Canadian dollars. An economic analysis was conducted with a discounted cash-flow before and after tax. The initial capital cost is estimated at US$471M including all infrastructures described earlier with a 10% contingency. The sustaining capital is estimated at US$238M over the life of mine.
The total payable products are estimated at 2,681,000 tonnes of chemical grade 5.56% Li2O concentrate, 783,000 tonnes of technical grade 6.16% Li2O concentrate, and 1,971 tonnes of 20% Ta2O5Â concentrate.
SPODUMENE PROCESS PLANT WITH A 4,600 TPD NOMINAL CAPACITY. OPEN PIT MINING RATE OF 1,610,000 TPY
A conventional truck and shovel open-pit approach was considered to mine the Rose Lithium-Tantalum Project’s Probable Mineral Reserves. The dimensions of the engineered pit design are approximately 1,620 m long x 900 m wide x 220 m deep.
The life of mine plan (LOM) proposes to mine 26.3 Mt of ore, 182.4 Mt of waste, and 10.9 Mt of overburden for a total of 219.6 Mt of material. The average stripping ratio is 7.3 tonnes of waste per tonne of ore. The nominal production rate is estimated at 4,600 tonnes per day and 350 operating days per year.
The mining operation production rate is set to approximately 15 Mt of material per year. An open pit mining schedule was planned and resulted in a mine life of 17 years.
Contract mining will be used for the removal of the overburden while Critical Elements will undertake the mining of all hard rock material with its own equipment fleet and operators.
The main production fleet will consist of one (1) backhoe excavator, one (1) electric front shovel, one (1) wheel loader, eight (8) haul trucks (65t each), seven (7) haul trucks (135t each), two (2) rotary drills, one (1) DTH drill, two (2) bulldozers, one (1) wheel dozer, two (2) graders, one (1) auxiliary excavator, one (1) auxiliary wheel loader, and two (2) water trucks.
The Rose project pit was designed with a 10 m single benching arrangement. A 57° inter-ramp angle and an overall pit slope angle of 55° were utilized for the ultimate pit design. A berm width of 7.0 m corresponding to the recommended overall slope angle was used. The pit slopes in overburden have a face ratio of 2.5:1 with a 10 m berm width.
The main in-pit haulage ramp is designed at 30.9 m wide to allow a double-lane traffic, except for the last benches at the pit bottom that are designed at 20.4 m wide for single lane traffic. A 2 m drainage ditch is included to allow for water drainage and pipe installation. The maximum gradient of the inner curvature of all ramp segments is 10%.
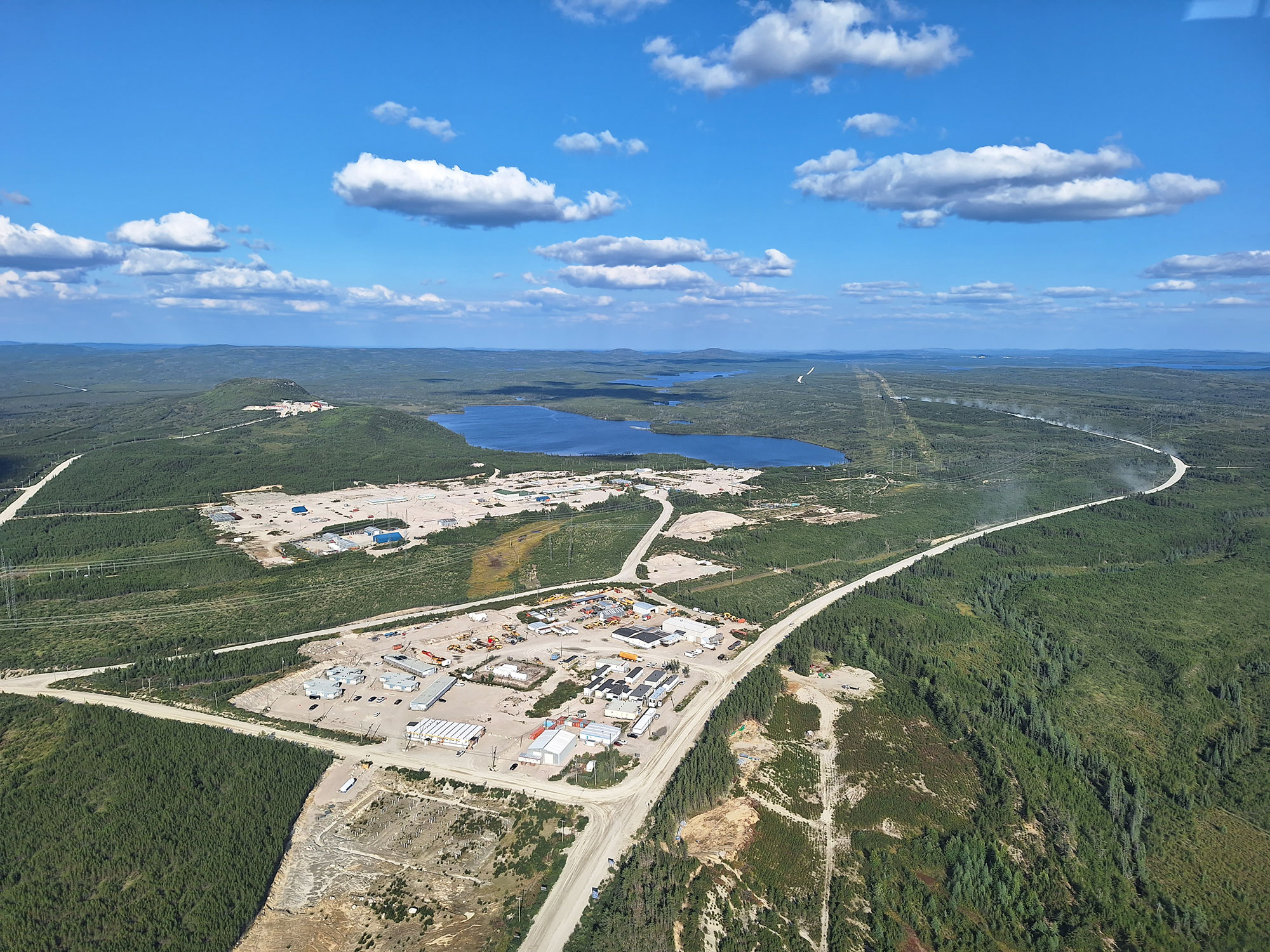
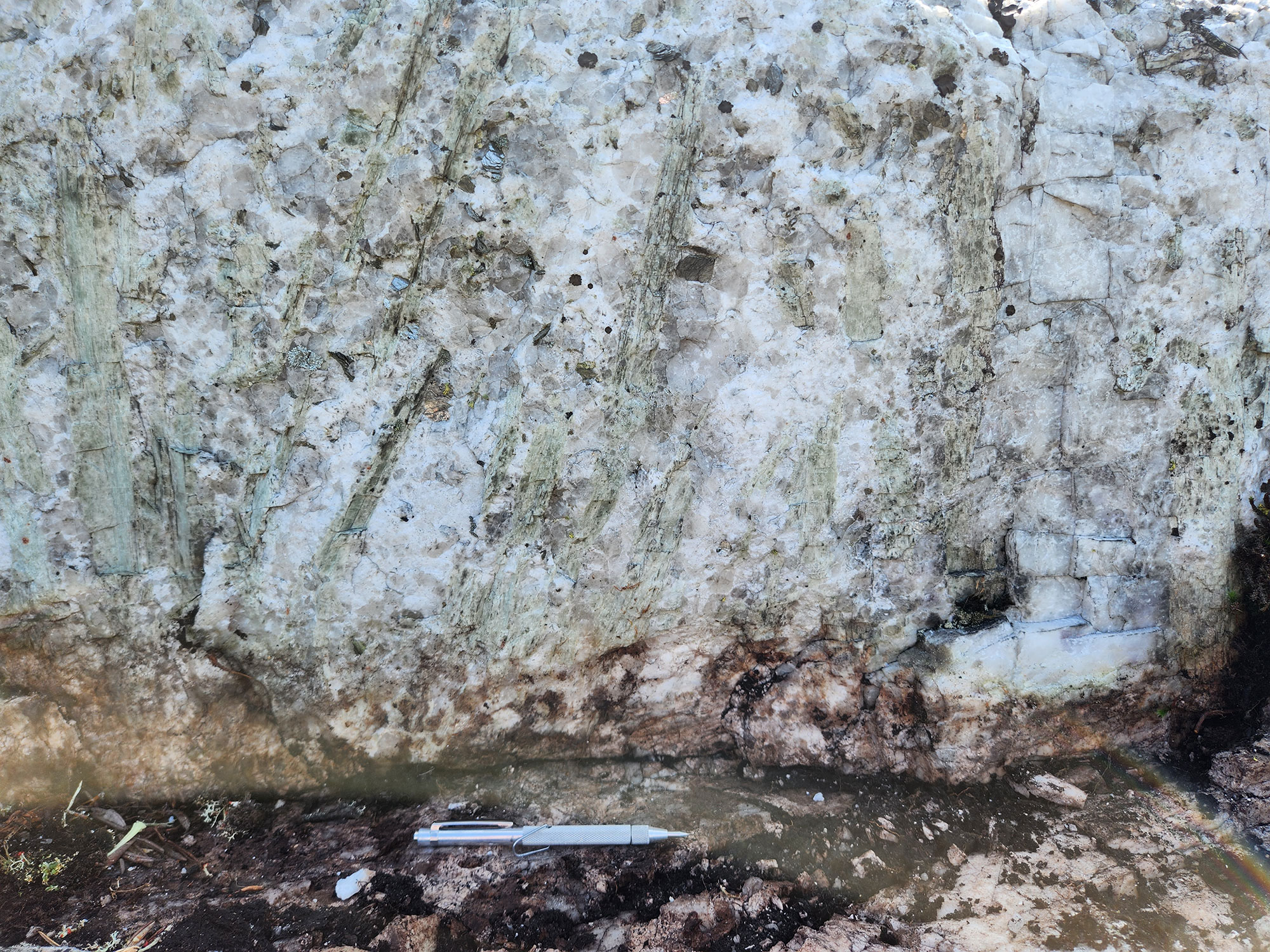
Feasibility Study assumes 84.8% and 87.4% recovery for technical and chemical grade lithium concentrates respectively
MINERAL PROCESSING
A standard froth flotation process will be utilized to produce technical grade and chemical grade lithium concentrates and a tantalum concentrate. The mineral process plant will consist of crushing, beneficiation, and dewatering areas.
- The technical grade lithium concentrate will grade 6.16% Li2O
- The chemical grade lithium concentrate will grade 5.56% Li2O.
- The tantalum concentrate will grade 20% Ta2O5.
The beneficiation process includes crushing, grinding, magnetic separation and flotation. The crushing circuit will consist of a jaw crusher and two (secondary and tertiary) cone crushers, and screens. The crushed ore will have a P80 of 13 mm and will be stockpiled in a 24-hour live capacity dome. The grinding circuit will consist of a ball mill operating in a closed circuit with a set of cyclones. The tantalum will first be recovered at a grade of 2.0% Ta2O5Â by high intensity magnetic separation then upgraded further to 20.0% Ta2O5Â by gravity separation. Tantalum concentrate will be thickened, filtered, dried to 1% moisture, and bagged for shipment. The lithium flotation circuit will include removal of slimes (particles less than 20 um) after magnetic separation followed by mica flotation, scrubbing, and spodumene flotation to the required grades. The spodumene concentrate will then be thickened, pressure filtered with a 5% moisture content, and stored in a dome with a capacity of 24 hours and then be transported by trucks and trains to the port. The flotation tailings will be thickened, vacuum filtered to 15% moisture or less, and trucked to the waste rock / tailings piles where it will be dry stacked.
- The spodumene plant will operate 24 hours per day, 7 days per week, and 52 weeks per year.
- The process plant was designed with an operating availability of 90%.
- The crushing circuit was designed using an operating availability of 50%.
- The plant has a capacity of 1,610,000 tonnes per year or 4,900 dry tonnes per day including availability.
The Feasibility Study assumes 84.8% and 87.4% recovery for technical and chemical grade lithium concentrates respectively and 54.4% minimum recovery for the tantalum concentrate. Process water will be recycled releasing minimal amounts to the retention pond and final effluent treatment plant.
Electrical transport line runs North-South over the eastern side of the Rose Property
The Project infrastructure includes site main access, services and haulage roads, explosive and detonator storage, a spodumene processing plant, a  maintenance facility, a warehouse, diesel and gasoline storage,  ore stockpile, waste rock and dry tailings co-disposal stockpile, overburden stockpile, main electrical substation and distribution, fresh and potable water supply, sewage, surface water management, final effluent treatment, communication system, gate house, and an administrative building. A camp complex will be built near the junction between the site access and Eastmain 1 road.
Electricity will be provided by Hydro-Québec. A 315 kV electrical transport line (L3176), owned by HydroQuébec, runs North-South over the eastern side of the Rose Property. It runs over the planned open pit. The portion running over the open pit representing 4.2 km will be rerouted to allow open pit operation.
Waste rock and tailings samples were analyzed, and both were considered to be non-potentially acid generating. The dry tailings and the waste rock will be stored in the same facility which has sufficient capacity for the life of mine. Rain and snow melt water will be collected in ditches and pumped to the water treatment plant.
The industrial pad has an area of 254,000 m2Â and will contain the process plant, the maintenance facility, warehouse, administration building, diesel and gasoline storage tanks, and all associated services. The ore pad will have an area of 105,000 m2Â where low-grade material may be stored.
The hydrology study has suggested that water inflow to the open pit is to be expected. To maximize pit slopes, water wells will be constructed around the pit periphery to lower the water table below the pit floor. One of these wells will be used to supply the site with fresh water. Water from the other wells will be directed to sedimentation ponds and treated, if necessary, before being released to the effluent.
Water from the waste rock / dry tailings stockpile, the open pit, the industrial pad, the overburden stockpile, and the roads will be collected in an equalization pond and treated before being released as final effluent.
The mine site will have a 2.7 km main access road from the Eastmain 1 road to the industrial pad.  Including the service roads, the site will total 16 km of roads.
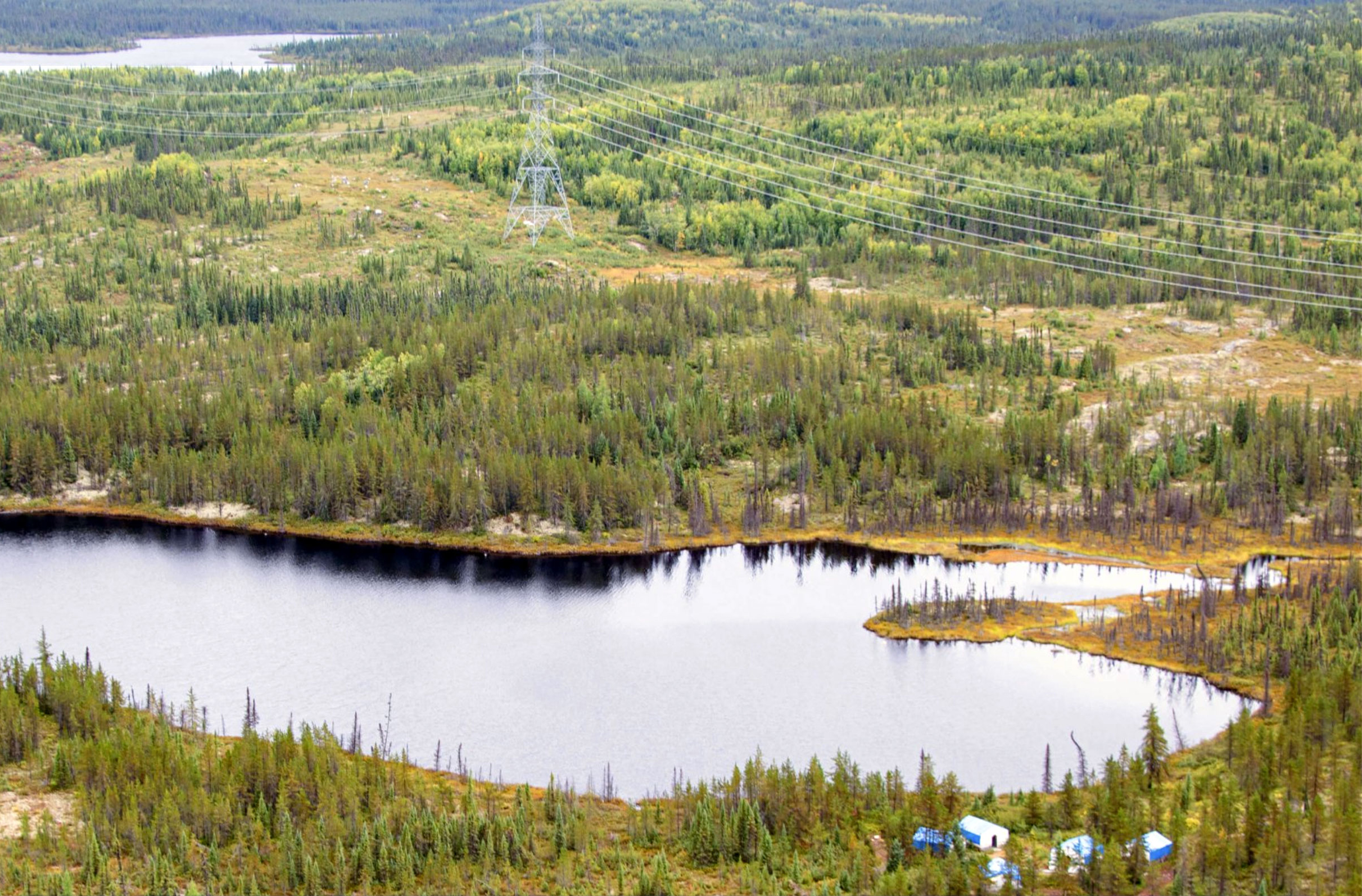